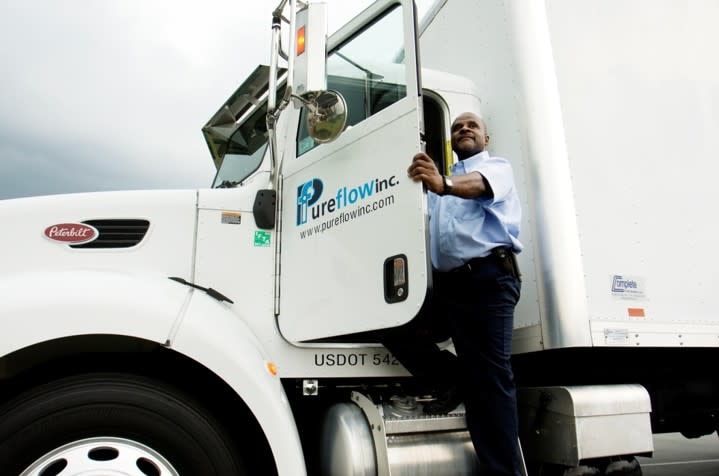
Reverse Osmosis Membrane Cleaning
By Steve Siverns & Stephen Boles | Pureflow, Inc.
Reverse osmosis (RO) membrane elements become fouled over time due to deposition on the membrane surface. The membrane becomes blocked and the RO permeate flow rate decreases. Often the permeate conductivity also increases due to minerals being concentrated even further at the membrane surface as they get trapped by the foulants.
Deposition can be mineral scale, silt, organic compounds or bacteria.
Mineral scale occurs in the last membranes of an RO system as this is where the minerals are most highly concentrated and thus most likely to precipitate. Scale is most commonly calcium carbonate, calcium sulfate, barium sulfate or silica (although other compounds can scale in some situations).
Silt fouling is most prevalent in the first membranes of an RO system. Silt particles are deposited on the membrane surface as the water permeates through the membrane.
Organic fouling is also most prevalent in the first membranes of an RO and the impact is very similar to silt fouling.
Bacterial fouling starts off the same way silt fouling does – deposition of individual bacteria on the membrane surface. However, bacteria proliferate over time and exude a “slime” to protect themselves. This slime further coats the membrane surface and can quickly foul the feed spacer and block the feed flow.
There are two general approaches to membrane cleaning. The first is predictive or preventive cleaning. With this approach, membrane cleaning is performed on a regular basis before the impacts of fouling become significant. Removing foulants before they become compacted makes it easier to clean the membrane surface and keep RO performance at design conditions.
A reactive cleaning approach waits until membrane performance is noticeably degraded before a cleaning is initiated. Often, operations staff wait until the RO can’t make enough permeate or until the permeate quality is at alarm limits before doing a cleaning; however, it is important to clean the membrane elements when any of the following conditions occur:
10-15% decrease in normalized permeate flow
10-15% increase in normalized permeate total dissolved solids (TDS)
10-15% increase in normalized pressure drop between feed and reject
It is important to use normalized parameters which account for ongoing variations in feed water conditions. Feed water TDS, water temperature, operating pressure and system recovery all affect permeate flow, permeate TDS and pressure drop making it difficult to determine if changes in any of these parameters are due to membrane fouling or to operating variations. Normalization calculations (available in spread sheet format from all membrane manufacturers) remove the impact of operating conditions to allow comparison of actual membrane performance over time.
Under no circumstances should systems be allowed to go beyond 20% changes in the normalized parameters. If fouling is allowed to proceed too far it can become extremely difficult or impossible to remove. In these situations membrane replacement is the only option.
Membrane cleaning is normally performed with the membrane elements left in their pressure housings (clean-in-place or CIP). A CIP skid is connected to the RO membrane array and cleaning solutions are circulated through the membrane elements. The CIP skid normally includes a tank, circulating pump, heater and cartridge filter. The tank allows mixing of the cleaning solution, the pump circulates the cleaning solution through the membranes, the heater warms the cleaning solution to accelerate cleaning action and the cartridge filter removes particulate matter released form the membranes.
Low pH (acid) cleaners remove most mineral scaling. High pH (caustic) cleaners remove organic and bacteria fouling. Detergents remove silt. Typically both a low pH and then a high pH cleaner are used in sequence. Results can often be obtained with generic chemicals but proprietary cleaners normally provide better results and cover a broader range of foulants.
Cleaning effectiveness requires sufficient flow through the membrane elements. Each element has a cleaning flow range specification. Too little flow leads to inefficient or insufficient cleaning. Too much flow can damage membrane elements. This is why the stages of an RO are cleaned independently from each other. A stage with 6 pressure housings requires much more flow than a stage with 2 pressure housings.
RO membranes must always be cleaned with cleaners at concentrations and temperatures that are compatible with the particular membranes installed. Each membrane has a published specification for cleaning conditions (with significant variation between manufacturers and membrane types).
To keep RO systems operating efficiently be sure to have a good understanding of the types of fouling that are likely to occur, monitor normalized performance regularly and clean the membranes proactively using the appropriate cleaning conditions.
Steve Siverns has been a partner of the Pureflow team since 2011. Steve has over 30 years of experience in design and troubleshooting of high purity water systems. He has his Masters of Engineering in Process Control from McMaster University in Hamilton, Canada and is PE registered in Ontario, Canada.
Stephen Boles is an Applications Engineer at Pureflow, Inc. and has been a member of the Pureflow team since 2007. Stephen has over 15 years of experience in designing, building, maintaining and troubleshooting high purity water systems. He has his B.S. in Mechanical Engineering from Cedarville University.
Article is re-printed with permission of Steve Siverns and Stephen Boles. Unauthorized reproduction of this article and/or use in any form is strictly prohibited without the expressed written consent of Pureflow, Inc.
Images
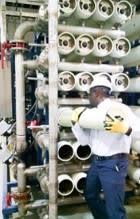
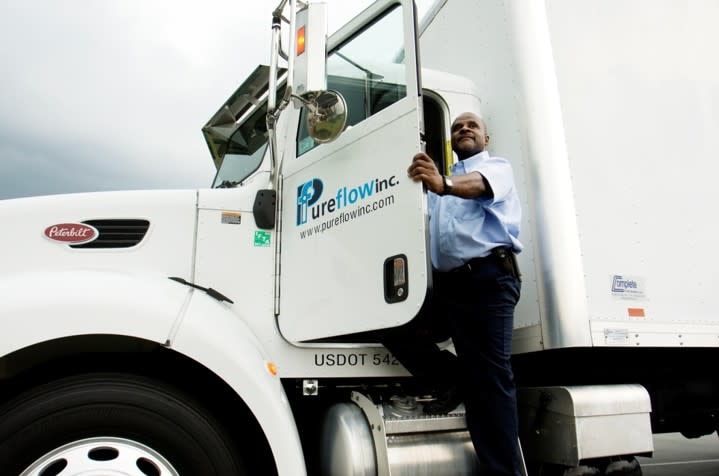